Kết quả nghiên cứu cho thấy, sau khi xử lý nhiệt, trên bề mặt lớp phủ có PPA thẩm thấu đã tạo thành các hợp chất phốt phát nhôm như AlPO4, Al(PO3)3 ở dạng tinh thể với các cấu trúc khác nhau…
Heat treatment and properties of nickel chromium alloy coating penetrated with aluminum phosphate
NGUYỄN VĂN TUẤN1,*, PHẠM THỊ HÀ1, PHẠM THỊ LÝ1, LÝ QUỐC CƯỜNG1, ĐINH THỊ MAI THANH1, LÊ THU QUÝ2
1 Viện Kỹ thuật nhiệt đới, Viện Hàn lâm Khoa học và Công nghệ Việt Nam, Số 18, Hoàng Quốc Việt, Cầu Giấy, Hà Nội.
*Email: vantuanvktnd@yahoo.com.vn
2 Phòng thí nghiệm trọng điểm Công nghệ Hàn và Xử lý bề mặt, Viện nghiên cứu cơ khí, Số 4 Phạm Văn Đồng, Cầu Giấy, Hà Nội
TÓM TẮT
Lớp phủ hợp kim niken-crôm (NiCr) chế tạo bằng phương pháp phun phủ hồ quang điện được thẩm thấu với dung dịch phốt phát nhôm (PPA) và xử lý nhiệt ở 800 oC. Các tính chất của lớp phủ như thành phần pha, độ xốp, độ bền mài mòn ma sát khô và độ bền ăn mòn mài mòn trong môi trường axit đã được khảo sát. Lớp phủ hợp kim NiCr không có PPA thẩm thấu cũng được khảo sát đồng thời nhằm mục đích so sánh. Kết quả nghiên cứu cho thấy, sau khi xử lý nhiệt, trên bề mặt lớp phủ có PPA thẩm thấu đã tạo thành các hợp chất phốt phát nhôm như AlPO4, Al(PO3)3 ở dạng tinh thể với các cấu trúc khác nhau. Độ xốp của lớp phủ có PPA thẩm thấu sau khi được xử lý nhiệt đã giảm khoảng 90%. Độ bền ăn mòn mài mòn trong dung dịch dịch axit H2SO4 chứa tác nhân gây xói mòn của lớp phủ có PPA thẩm thấu cao hơn khoảng 32% so với lớp phủ không có PPA thẩm thấu. Kết quả này mở ra hướng ứng dụng của lớp phủ hợp kim NiCr chế tạo bằng công nghệ phun phủ hồ quang điện trong các ngành công nghiệp khai thác khoảng sản, đặc biệt là ngành công nghiệp khai thác than.
Từ khóa: phun phủ hồ quang điện, lớp phủ hợp kim NiCr, xử lý nhiệt, phốt phát nhôm, ăn mòn, mài mòn
ABSTRACT
The nickel chromium alloy coating (NiCr) which was prepared by electric arc thermal spray was penetrated with aluminium phosphate solution and heat-treated at 800 oC. Properties of coating as phase composition, the coating’s porosity, abrasive wear resistance and corrosion and wear resistance in the acid media was studied. The NiCr coating which was not penetrated with aluminium phosphate solution were studied which to compare. The results indicated that, after the treatment on the coating’s surface was penetrated with aluminium phosphate solution pre- sent other crystalline compounds of aluminium phosphate as AlPO4, Al(PO3)3 After the coating was penetrated with aluminium phosphate solution and heat-treated, about 90% of the pores inside of the coating were filled. The corrosion and wear resistance in the H2SO4 acid solution containing erosion agent cause for the coating which was penetrated with aluminium phosphate solution increase about 35% in comparison with the coating which was not penetrated. The results in this study open the way to the application of NiCr alloy coating prepared by by electric arc thermal spray in the mining industries, particularly is the coal mining industry.
Key words: electric arc thermal spray, niken-crom alloy coating, heat-treated, aluminium phosphate, corrosion, wear
1. ĐẶT VẤN ĐỀ
Lớp phủ NiCr chế tạo bằng công nghệ phun phủ dùng hồ quang điện có độ xốp khá cao khoảng 11,5% [1]. Điều này đã làm ảnh hưởng đến các tính chất của lớp phủ, đặc biệt là khả năng chống ăn mòn của lớp phủ.
Để nâng cao khả năng chống ăn mòn của lớp phủ NiCr thì việc xử lý làm giảm độ xốp của lớp phủ là cần thiết. Lớp phủ có thể được xử lý bằng nhiều phương pháp khác nhau như bằng laze, lắng đọng hơi hóa học kim loại-chất hữu cơ, lắng đọng hơi hóa học ở nhiệt độ cao, thấm hơi hóa học,… Tuy nhiên, các phương pháp này đòi hỏi về thiết bị rất phức tạp và đắt tiền [2]. Do đó, việc xử lý các lỗ xốp của các lớp phủ thường được thực hiện bằng phương pháp xử lý nhiệt hoặc phương pháp thẩm thấu với các hợp chất hóa học trong đó có PPA. Trong nghiên cứu này, chúng tôi đã tiến hành xử lý nhiệt và khảo sát các tính chất của lớp phủ có và không PPA thẩm thấu.
Lớp phủ hợp kim NiCr có và không có PPA thẩm thấu được xử lý nhiệt ở 800 oC. Dung dịch PPA cũng được xử lý ở 800 oC cùng với các mẫu lớp phủ. Các tính chất của lớp phủ được khảo sát bao gồm: thành phần pha, độ xốp, độ bền mài mòn ma sát khô và độ bền ăn mòn mài mòn trong môi trường dung dịch axit.
2. THỰC NGHIỆM
2.1. Chuẩn bị mẫu thí nghiệm
Hợp kim NiCr dưới dạng dây có đường kính 2 mm với thành phần hóa học là: 79,39% Ni, 18,16% Cr, 0,9% Si, 0,26% Ti, 0,73% Mn, 0,56% Fe được phun lên tấm thép hình tròn đường kính 50 x 3 mm với chiều dày lớp phủ khoảng 1000 µm sử dụng thiết bị OSU Hessler 300A (Đức).
Dung dịch PPA được tổng hợp từ axít phốtphoric (H3PO4 85%) và bột nhôm hydroxit (Al(OH)3) với tỷ lệ số mol P/Al = 2,3. Quá trình tổng hợp dung dịch PPA được thực hiện trong khoảng nhiệt độ 110 ÷ 120 oC. Sau khi tổng hợp, dung dịch PPA được bổ sung thêm nước với hàm lượng 20%, tiếp theo, dung dịch PPA được tiến hành đo độ nhớt và khối lượng riêng. Độ nhớt và khối lượng riêng của dung dịch PPA đo được lần lượt là 177,36 s (độ nhớt của dung dịch được đo bằng phễu đo độ nhớt BZ4 [3]) và 1,58 g/cm3.
Dung dịch PPA sau khi quét lên bề mặt lớp phủ của mẫu cần khảo sát được để ổn định sau 12 giờ ở nhiệt độ phòng cùng vời dung dịch PPA không được quét lên lớp phủ trước khi đưa đi xử lý nhiệt. Lớp phủ hợp kim NiCr không có PPA thẩm thấu cũng được xử lý nhiệt ở 800 oC cùng với các mẫu nêu trên.
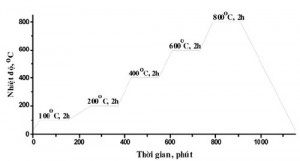
2.2. Xử lý nhiệt
Các mẫu thí nghiệm được tiến hành xử lý nhiệt ở 800 oC trong lò nung NABERTHERM theo quy trình xử lý nhiệt được đưa ra trên hình 1 [2, 4]. Mẫu lớp phủ có và không có PPA thẩm thấu sau khi tiến hành xử lý nhiệt ở 800 oC có ký hiệu tương ứng là NA8 và NC8.
2.3. Phương pháp nghiên cứu
Thành phần pha tinh thể được xác định bằng phương pháp nhiễu xạ Rơnghen (XRD) trên thiết bị phân tích Rơnghen D5005 với bức xạ Cu-Kα, góc quét 2θ từ 10o đến khoảng 60-70o, bước quét 0,02o/s.
Độ xốp của các lớp phủ được xác định bằng phương pháp phân tích ảnh trên cấu trúc mặt cắt ngang dưới kính hiển vi quang học Axiovert 40 Mat có kèm theo phần mềm phân tích thành phần pha AxioVision (Đức). Quy trình chuẩn bị mẫu và phân tích được thực hiện theo tiêu chuẩn ASTM E2109 -14 [5].
Độ cứng tế vi (HV) của lớp phủ được đo tại 10 điểm trên bề mặt của lớp phủ đã được mài nhẵn, dưới tải trọng 300 g, thời gian lưu lực 15 s [6].
Độ bền mài mòn ma sát khô được đo theo tiêu chuẩn ASTM G99-10 [7] trên thiết bị thử mài mòn TE 97 Friction and Wear Demonstrator – Viện cơ khí năng lượng và Mỏ với các thông số thử nghiệm như sau: lực tác dụng 30 N, tốc độ quay của mẫu 382 vòng/phút, thời gian đo 15 phút [8-10].
Thử nghiệm ăn mòn mài mòn trong dung dịch axit H2SO4 pH2 chứa 3% hạt gây xói mòn SiO2 (≈100µm) với tốc độ dòng chảy của dung dịch là 4 m/s [11-14].
3. KẾT QUẢ VÀ THẢO LUẬN
3.1. Thành phần pha
Giản đồ XRD thể hiện trên hình 2 là kết quả phân tích thành phân pha có trong hỗn hợp PPA sau khi được xử lý nhiệt ở 800 oC.
Kết quả phân tích cho thấy, sau khi xử lý nhiệt, trong hỗn hợp PPA tồn tại chủ yếu 2 loại tinh thể Al(PO3)3(cubic) và AlPO4 (hexalgonal). Tinh thể Al(PO3)3(N), cũng được tìm thấy trong hỗn hợp PPA nhưng với cường độ tín hiệu yếu hơn nhiều so với cường độ tín hiệu của các tinh thể Al(PO3)3(cubic) và AlPO4 (hexalgonal).
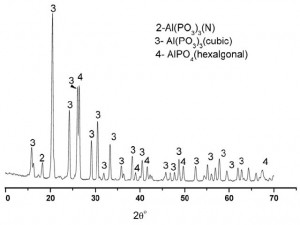
Thành phần pha tinh thể hình thành trên bề mặt mẫu lớp phủ có PPA thẩm thấu sau khi được xử lý nhiệt ở 800 oC (NA8) cũng được xác định bằng phương pháp XRD. Kết quả phân tích được thể hiện trên hình 3.
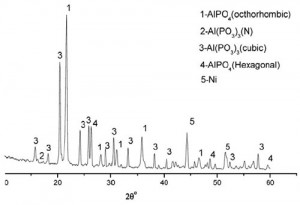
Kết quả phân tích cho thấy, các pha tinh thể Al(PO3)3(N), Al(PO3)3 (cubic), AlPO4 (Hexagonal) có trong PPA cũng được tìm thấy trên bề mặt lớp phủ, tuy nhiên, cường độ tín hiệu của các pha tinh thể này đã có sự thay đổi so với PPA không có lớp phủ. Kết quả khảo sát cho thấy tinh thể AlPO4 (octhorhombic) trên bề mặt lớp phủ hợp kim NiCr có cường độ tín hiệu rất mạnh, trong khi đó, tinh thể này không được phát hiện trong hỗn hợp PPA không có lớp phủ. Điều đó chứng tỏ rằng do ảnh hưởng của lớp phủ NiCr đã làm cho cấu trúc của tinh thể AlPO4 có sự biến đổi. Ngoài ra, do chịu ảnh hưởng của lớp phủ mà tinh thể Al(PO3)3 cũng có sự thay đổi về cấu trúc. Cụ thể, trong hỗn hợp PPA, tinh thể Al(PO3)3(N) xuất hiện với cường độ tín hiệu khá rõ nét, trong khi đó, trên bề mặt lớp phủ, tinh thể này xuất hiện với cường độ rất yếu. Tinh thể Cr không được phát hiện trên bề mặt lớp phủ do PPA trên bề mặt lớp phủ còn khá dày đã cản trở sự phát hiện của tinh thể này có trong lớp phủ. Các kết quả khảo sát cũng cho thấy, trên bề mặt lớp phủ không thấy xuất hiện các tinh thể của hợp chất giữa Ni với PPA. Điều này chứng tỏ rằng, sự tương tác hóa học giữa lớp phủ và PPA đã không xảy ra.
3.2. Độ xốp của lớp phủ
Độ xốp của lớp phủ được xác định bằng phương pháp phân tích ảnh cấu trúc mặt cắt ngang theo tiêu chuẩn ASTM E2109 -14, theo đó ảnh mặt cắt ngang của các mẫu được chụp tại 5 vị trí với độ phóng đại x100 bằng kính hiển vi quang học.
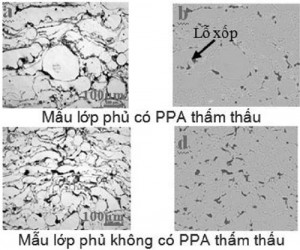
Hình 4 là ảnh được chụp tại 1 vị trí trên mặt cắt ngang của mẫu lớp phủ có và không có PPA thẩm thấu với cùng độ phóng đại x100. Ảnh được thể hiện trên hình 4 (b,d) thì màu xanh đặc trưng cho các lỗ xốp có trong lớp phủ đã được xử lý và màu đỏ là các lỗ xốp còn lại trong lớp phủ.
Kết quả phân tích cho thấy, sau khi được xử lý nhiệt ở 800 oC, độ xốp của lớp phủ không có PPA thẩm thấu còn khá cao so với lớp phủ có PPA thẩm thấu. Cụ thể, độ xốp của lớp phủ không có PPA thẩm thấu là 3,21 %. Trong khi đó, độ xốp của lớp phủ có PPA thẩm thấu là 1,41%. Như vậy có thể thấy, sau khi được thẩm thấu với PPA, độ xốp của lớp phủ đã giảm đến hơn 2 lần so với mẫu lớp phủ không được thẩm thấu với PPA.
3.3. Độ bền mài mòn ma sát khô và độ cứng tế vi
Độ bền mài mòn ma sát khô của lớp phủ hợp kim NiCr được đánh giá theo tiêu chuẩn ASTM G99-10 [7]. Phương pháp đo tổn hao khối lượng được sử dụng để xác định khả năng chịu mài mòn của các mẫu. Kết quả thử nghiệm khả năng chịu mài mòn của các mẫu được đưa ra trên hình 5. Kết quả nghiên cứu cho thấy, tổn hao khối lượng của lớp phủ có và không có PPA thẩm thấu tương ứng là 255,5 mg và 328,5 mg. Điều này chứng tỏ rằng, sau khi được thẩm thấu với PPA, độ xốp của lớp phủ thấp, cùng với sự xuất hiện của các tinh thể PPA trên bề mặt lớp phủ, đã làm khả năng chịu mài mòn của lớp phủ tăng gần 30% so với lớp phủ không được thẩm thấu với PP.
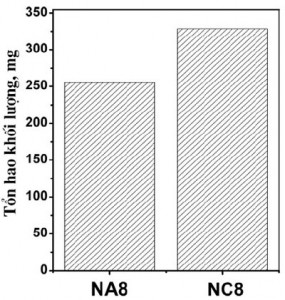
Các kết quả đo độ cứng HV trên bề mặt của các mẫu lớp phủ cho thấy, độ cứng không có sự khác nhau nhiều giữa lớp phủ có và không có PPA thẩm thấu. Cụ thể, độ cứng HV 0.3 của mẫu lớp phủ NA8 và NC8 lần lượt là 272 và 270. Kết quả này cho thấy rằng, sự suy giảm độ xốp, cùng với sự hình thành các tinh thể PPA trên bề mặt là yếu tố chính góp phần làm tăng khả năng chịu mài mòn của lớp phủ.
3.4. Độ bền ăn mòn mài mòn
Trên cơ sở tham khảo các tài liệu [11-14], chúng tôi đã tiến hành thử nghiệm độ bền ăn mòn mài mòn của các lớp phủ trong dung dịch H2SO4 pH2 có chứa các hạt rắn SiO2 gây xói mòn với hàm lượng 3%, chuyển động với tốc độ dòng chảy là 4 m/s.
Khả năng chịu mài mòn của lớp phủ trong môi trường dung dịch axit được đánh giá thông qua việc xác định sự thay đổi chiều dày của mẫu thử theo thời gian, theo đó, chiều dày của lớp phủ trong quá trình thử nghiệm được đo định kỳ theo thời gian tại bằng thiết bị Mitutoyo DIGI-DERM 745 (Nhật Bản). Giá trị chiều dày nhận được là giá trị trung bình của 5 lần đo. Kết quả khảo sát được thể hiện trên hình 6.
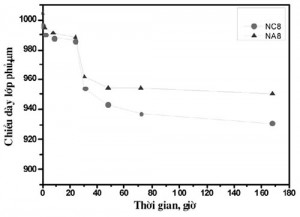
Kết quả khảo sát cho thấy, chiều dày của các mẫu lớp phủ giảm theo thời gian thử nghiệm. Tuy nhiên, sự suy giảm chiều dày của mẫu NC8 lớn hơn nhiều so với mẫu NA8, đặc biệt là sau khoảng thời gian đầu đến 30 giờ thử nghiệm.
Sau 72 giờ thử nghiệm kết quả khảo sát cho thấy, chiều dày mẫu NC8 đo được vẫn tiếp tục giảm, trong khi đó chiều dày các mẫu NA8 gần như không đổi. Sau 168 giờ thử nghiệm, chiều dày của mẫu NA8 và NC8 đo được giảm tương ứng 44 µm và 65 µm. Như vậy, chiều dày của mẫu lớp phủ NA8 có sự suy giảm thấp hơn khoảng 32% so với lớp phủ NC8. Kết quả này cho thấy, sự hình thành các tinh thể của các hợp chất PPA (AlPO4, Al(PO3)3) cùng với quá trình thẩm thấu và điền đầy các lỗ xốp có trong lớp phủ của PPA đã góp phần cải thiện đáng kể khả năng chịu mài mòn của lớp phủ cả ở điều kiện mài mòn ma sát khô và mai mòn do dòng chảy của dung dịch có chứa các hạt SiO2 gấy xói mòn.
Khả năng chống ăn mòn của lớp phủ trong môi trường dung dịch H2SO4 pH2 chứa tác nhân gây xói mòn SiO2 hàm lượng 3% được xác định bằng phương pháp đo phân cực điện hóa theo tiêu chuẩn ASTM G59. Bảng 1 và 2 dưới đây đưa ra kết quả về các thông số ăn mòn được xác định từ các đường cong phân cực trên hình 7 và hình 8.
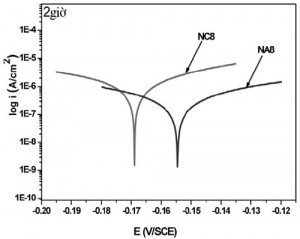
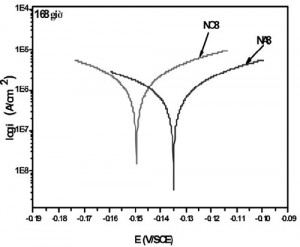
Kết quả khảo sát cho thấy, sau 168 giờ thử nghiệm, mật độ dòng ăn mòn của mẫu NA8 là 1,0603 µA/cm2, thấp hơn khá nhiều so với mẫu NC8 (1,8494 µA/cm2). Kết quả này cho thấy, độ xốp của lớp phủ thấp cùng với sự hình thành các pha tinh thể AlPO4, Al(PO3)3 trên bề mặt mẫu lớp phủ không những đã cải thiện nhiều khả năng chịu mài mòn mà còn cải thiện đáng kể khả năng chống ăn mòn cho lớp phủ.
Bảng 1. Các thông số ăn mòn của các lớp phủ xác định sau 2 giờ thử nghiệm
Mẫu | Sau 2 giờ thử nghiệm | ||
Rp(kΩ) | icorr (μA/cm2) | Ecorr (mV/SCE) | |
NC8 | 9,2096 | 1,0183 | -172 |
NA8 | 34,021 | 0,2689 | -158 |
Bảng 2. Các thông số ăn mòn của các lớp phủ xác định sau 168 giờ thử nghiệm
Mẫu | Sau168 giờ thử nghiêm | ||
Rp(kΩcm2) | icorr(μA/cm2) | Ecorr(mV/SCE) | |
NC8 | 5,3956 | 1,8494 | -154 |
NA8 | 9,7439 | 1,0603 | -141 |
Mật độ dòng ăn mòn sau 168 giờ tăng khá mạnh so với với thời điểm sau 2 giờ thử nghiệm ở cả 2 mẫu. Cụ thể, đối với mẫu NC8 mật độ dòng ăn mòn đo tại thời điểm sau 2 giờ và 168 giờ thử nghiệm tương ứng là 1,0183 và 1,8494 µA/cm2, thay đổi trên 80%. Đối với mẫu NA8 mật độ dòng ăn mòn đo tại các thời điểm sau 2 giờ và 168 giờ tương ứng là 0,2689 và 1,0603 µA/cm2, thay đổi đến gần 300%. Kết quả này được giải thích như sau: Mật độ dòng ăn mòn tăng theo thời thử nghiệm ở cả 2 mẫu là do chiều dày lớp phủ giảm dần và quá trình thấm thấu dung dịch ăn mòn ngày càng sâu vào trong lớp phủ khi thời gian thử nghiệm tăng lên. Đối với mẫu NA8, thời gian đầu, sau khoảng 2 giờ thử nghiệm, PPA vẫn còn nhiều trên bề mặt đã hạn chế đáng kế tốc độ ăn mòn của lớp phủ. Sau 168 giờ thử nghiệm, lượng PPA trên bề mặt mẫu mất đi dần do quá trình xói mòn đã làm cho tốc độ ăn mòn của lớp phủ đo tại thời điểm sau 168 giờ thử nghiệm tăng khá mạnh so với thời điểm sau 2 giờ thử nghiệm.
4. KẾT LUẬN
Một số kết luận được rút ra từ các kết quả khảo sát trong nghiên cứu này như sau:
– Sau khi xử lý nhiệt ở 800 oC, cấu trúc của các tinh thể AlPO4 và Al(PO3)3 có sự thay đổi khi chịu sự ảnh hưởng của lớp phủ hợp kim NiCr và nhiệt độ.
– Sau khi thẩm thấu với dung dịch PPA và xử lý nhiệt, độ xốp của lớp phủ đã giảm đi khoảng 2 lần so với lớp phủ không được thẩm thấu.
– Độ bền mài mòn của lớp phủ sau khi thẩm thấu với PPA trong cả 2 môi trường khô (mài mòn do ma sát) và ướt đều tăng so với lớp phủ không được thẩm thấu với PPA. Cụ thể, trong môi trường khô, độ bền mài mòn tăng hơn gần 30% và trong môi trường ướt, độ bền mài mòn tăng trên 30%.
– Khả năng chống ăn mòn trong môi trường dung dịch chứa các hạt gây xói mòn cũng được cải thiện đáng kể sau khi lớp phủ được thẩm thấu với PPA.
LỜI CẢM ƠN
Nghiên cứu này đã được hoàn thành với sự hỗ trợ kinh phí của đề tài cơ sở cấp Viện Kỹ thuật nhiệt đới – Viện Hàn lâm Khoa học và Công nghệ Việt Nam năm 2013.
TÀI LIỆU TRÍCH DẪN
- Lê Thu Quý, Nghiên cứu chế tạo lớp phủ hợp kim niken crôm bằng công nghệ phun phủ hồ quang điện để bảo vệ chống ăn mòn cho các chí tiết máy bơm công nghiệp làm việc trong môi trường axít, đề tài nghiên cứu khoa học công nghệ cấp Viện Hàn lâm Khoa học và Công nghệ Việt Nam, mã số VAST 04.01/11-12
- J. Knuuttila, P. Sorsa and T. Mäntylä, Sealing of thermal spray coatings by impregnation”, ASM International – JTTEE5 8:249-257 (1999)
- TCVN 2092:2008, Sơn và vecni. Xác định thời gian chảy bằng phễu chảy
- E.M. Leivo, M.S. Vippola, P.P.A. Sorsa, P.M. Vuoristo and T.A. Mantyla, Wear and corrosion properties of plasma sprayed Al2O3 and Cr2O3 coatings sealed by aluminum phosphates, Journal of Thermal Spray Technology, 6(2), 205 (1997)
- ASTM E2109-01, Test Methods for Determining Area Percentage Porosity in Thermal Sprayed Coatings
- B. M. Amokrane, A.Abdelhamid, M. Youcef, B. Abderrahim, O.Nedjeddine, M.Ahmed, Microstructural and Mechanical Properties of Ni-Base Thermal Spray Coatings Deposited by Flame Spraying, Metallurgical and materials trasactions B, 42B, 932-938 (2011)
- ASTM G99-10, Standard Test Method for Wear Testing with a Pin-on-Disk Apparatus
- N. P. Abbade, S. J. Crnkovic, Sand – water slurry erosion of API. 5L X65 pipe steel as quenched from inter- crid temperature, Tribology International, 33, 811-816 (2000)
- L.Thakur and N.Arora, Sliding and Abrasive Wear Behavior of WC-CoCr Coatings with Different Carbide Sizes, Materials Engineering and Performance (2012)
- Y.Ishikawa, S.Kuroda, J.Kawakita, Y.Sakamoto, M.Takaya, Sliding wear properties of HVOF sprayed WC-20%Cr3C2-7%Ni cermet coatings, Surface & Coatings Technology 201, 4718-4727 (2007)
- H.S.Sidhu, B.S. Sidhu, and S. Prakash, Comparative Characteristic and Erosion Behavior of NiCr Coatings Deposited by Various High-Velocity Oxifuel Spray Processes, Materials Engineering and Performance 15(6), 699-703 (2006)
- Q. Fang, H. Xu, P. S. Sidky, M. G. Hocking, Erosion of ceramic materials by sand/water slurry jet, Wear, 224, 183-193 (1999)
- S. K. Shrestha, Corrosion and erosion corrosion of high velocity Oxi-Fuel (HVOF) Sprayed NiCrSiB coating, University of Glasgow, Russia (2000)
- Đoàn Đình Phương, Nghiên cứu phát triển hợp kim hệ Fe-Cr-C làm việc trong điều kiện mài mòn và ăn mòn xâm thực, Luận án Tiến sĩ Khoa học Vật liệu, Viện Khoa học Vật liệu (2007)
- ASTM G59-97(2014), Standard Test Method for Conducting Potentiodynamic Polarization Resistance Measurements.