The purpose of this study is to deposit ZrN thin films by cathodic arc plasma evaporation and to investigate the improvement of corrosion resistance of the coated film on SKD11 steel…
Effect of nitrogen flow rate on microstructure and properties of ZrN thin films grown by cathodic arc plasma evaporation
TRỊNH VĂN TRUNG1,2,*, NGUYỄN VĂN THÀNH3
1 School of Materials Science and Engineering, Hanoi University of Science and Technology, No. 1, Dai Co Viet, Hai Ba Trung, Hanoi, Viet Nam
2 Vietnam – Japan International Institute for Science of Technology, Hanoi University of Science and Technology, No. 1, Dai Co Viet, Hai Ba Trung, Hanoi, Viet Nam
3 Laboratory of Technology and Casting alloys, Research Institute of Technology for Machinery, No. 25, Vu Ngoc Phan, Dong Da, Ha Noi, Viet Nam
*Email: trung.trinhvan@hust.edu.vn
Ngày nhận bài: 19/7/2018, Ngày duyệt đăng: 26/9/2018
TÓM TẮT
Màng mỏng ZrN được tạo trên đế thép SKD11 bằng phương pháp bốc bay hồ quang plasma catôt. Ảnh hưởng của lưu lượng khí nitơ đến cấu trúc, độ cứng và khả năng chống ăn mòn của màng được khảo sát bằng các phương pháp như XRD, SEM kết hợp EDS, đo độ cứng tế vi và đo ăn mòn điện hóa. Kết quả khảo sát cho thấy màng mỏng đơn pha ZrN với định hướng ưu tiên theo mặt tinh thể (200) được tạo thành trên đế thép SKD11. Màng phủ được hình thành cùng các hạt micro. Độ cứng có thể đạt đến giá trị 2288 HV ở lưu lượng khí nitơ là 300 sccm. Kiểm tra ăn mòn điện hóa cho thấy lớp phủ ZrN đã cải thiện đáng kể đặc tính chống ăn mòn trong dung dịch NaCl 3 % với hiệu suất bảo vệ, Pi, lên tới 87 %.
Từ khóa: Màng mỏng ZrN, hồ quang plasma catôt, lưu lượng khí nitơ, chống ăn mòn, thép SKD11.
ABSTRACT
Thin films of ZrN were grown on SKD11 steel by the method of cathodic arc plasma evaporation. The influences of nitrogen flow rate on the microstructure, hardness and corrosion resistance of the films were investigated by XRD, SEM & EDS, microhardness, and electrochemical test. The result showed that the single phase of ZrN films with the preferred orientation of (200) was formed on the SKD11 substrate. The coated film was deposited with micro-droplets. High hardness value (2288 HV) was archived at the nitrogen flow rate of 300 sccm. The electro- chemical test demonstrated that the ZrN coating can greatly improve the corrosion-resistant property in 3 % NaCl solution with protective efficiency, Pi, up to 87 %.
Keywords: ZrN thin film, cathodic arc plasma, nitrogen flow rate, corrosion resistance, SKD11 steel.
1. INTRODUCTION
Recently, zirconium nitride (ZrN) films, owing to their low resistivity, good corrosion resistance, high mechanical properties, and gold-like color, etc. have attracted increasing interests for various applications such as protective coatings on cutting tools, diffusion barrier in integrated circuits, or as a decorative coating [1]. It has been reported that the ZrN coating showed higher corrosion protection ability compared to that of TiN coating deposit- ed on 316L stainless steel [2].
In recent years, cathodic arc plasma evapora- tion (CAPE) technique is most widely applied in industrial processes, because of excellent adhe- sive properties with various substrates also due to high current density, ionization ratio and flexibility of target arrangements [3, 4]. This technique can be used to deposit various transition metal nitride thin films such as TiN, CrN, ZrN, TiCN, TiAlN, etc [5]. However, because Zr has a higher melting point, a lower vapor pressure, and higher contam- ination susceptibility by oxygen and carbon, suc- cessful deposition of decent quality the ZrN film poses greater difficult than TiN or CrN films [6]. The microstructure and properties of ZrN thin film strongly depend on experimental parameters such as substrate bias voltage [7], substrate tempera- ture [4], nitrogen flow rate [8], substrate-target orientation [9], etc. J. H. Huang and et al. studied the effect of nitrogen flow rate on the structure and mechanical properties of ZrN thin films deposited on Si(100) and stainless steel substrates by using hollow cathode discharge ion-plating (HCD-IP). The result showed that the N/Zr ratio and grain size increase with increasing nitrogen flow rate. The hardness of the nanocrystalline ZrN film is only slightly varied with nitrogen flow rate [8]. The effect of the nitrogen flow rate on the corrosion resistance of ZrN thin films grown by cathodic arc plasma evaporation is still needed to investigate.
The purpose of this study is to deposit ZrN thin films by cathodic arc plasma evaporation and to investigate the improvement of corrosion resistance of the coated film on SKD11 steel.
2. EXPERIMENTAL
The ZrN coatings were deposited on polished SKD11 steels substrates (18 6 mm) by using a cathodic arc evaporation (CAE) system, Dreva-400. The SKD11 substrates were analyzed by optical emission spectrometer (OES), had a com- position of33 %C, 11.28 %Cr, 0.38 Mo, 0.18V, and the balance being Fe. Before deposition, the SKD11 specimens were heat treated as follows: austempering at 1020 °C for 30 minutes, quenching by oil, and then tempering at 550 °C for 2 hours to archive the hardness of about 60 HRC (~ 698 HV). Then the specimens were ground by 100, 240, 400, 600, 800, and 1000 grit abrasive papers and polished with Cr2O3 emulsion. Finally, the specimens were ultrasonically cleaned in acetone, alcohol, and distilled water successively and dried.
To synthesize the ZrN film, the SKD11 specimens were mounted in the middle of the chamber. The working chamber was evacuated to a pressure of 2.4×10−4 mbar. Meanwhile, the substrates were gradually heated to 300 °C, and then Ar gas with the flow rate of 60 sccm was introduced into the chamber. The SKD11 specimens were biased to −200 V for 15 min to sputter clean its surface with a hollow cathode current of 100 A. After that, Ar gas flow rate reduced to 10 sccm and nitrogen gas (with the flow rate of 250, 300, and 350 sccm) was introduced as reactive gases to deposit ZrN coatings. The deposition parameters are shown in Table 1.
Table 1. Experimental deposition conditions of ZrN coatings by cathodic arc deposition.
Target | Zr (99.9%) |
Reactive gas | N2 |
Nitrogen flow rate | 250, 300, and 350 sccm |
Substrate bias voltage | – 20 V |
Source to substrate distance | 200 mm |
Evaporator current | 120 A |
Reactive gas pressure | 2.4×10-4 mbar |
Chamber temperature | 300 °C |
Deposition time | 10 min |
The coating hardness was evaluated using the Vickers measurement technique. Hardness mea- surements were performed by placing Vickers indentations on the coated surface for 15 s, and the indentation loads were 10 N. The surface morphology was studied using a Nova Nanosem 450 Scanning Electron Microscope (SEM). Phase composition of the films was determined by X-ray diffraction (XRD) using CuKα radiation. The value of texture coefficient of hkl crystallographic planes, Tc(hkl), was calculated using the equation:
where I(hkl) is the intensity from (hkl) planes in the specimen, and Io(hkl) is the standard intensity of the corresponding plane given in the PDF data, and n is the total number of diffraction peaks. The Tc(hkl) is proportional to the number of grains that are oriented with this (hkl) plane parallel to the surface of the specimen [10].
Tafel curves were obtained through a potentiostat/galvanostat controlled from a computer. The electrochemical measurements were performed in a standard three-electrode cell with platinum counter electrode and a saturated calomel elec- trode as the reference electrode. The electrolyte is 3 % NaCl solution. All the corrosion experiments were conducted at 37 °C ± 0.5 °C. After each potentiodynamic polarization test, the corrosion potential, Ecorr, and the corrosion current density, Icorr, can be determined by Tafel plot.
3. RESULTS AND DISCUSSION

Fig. 1 shows the top-view SEM image of asdeposited ZrN film with micro-droplets deposited on the SKD11 substrate. The size of the droplets on the ZrN surface varies from part of a micrometer up to 1 µm. The chemical composition of the film is 49.4 Zr – 48.6 N – 1.7 Fe – 0.3 Cr (in at. %), according to the EDS analysis.

Fig. 2 shows diffraction patterns of the film grown on the SKD11 substrate with different nitro- gen flow rates. Zirconium nitride (ZrN) is mostly showing cubic crystallographic phase and the diffraction planes at 2θ ≅ 33.87o, 39.27o, 56.94o, 67.76o, and 71.45o correspond to cubic zirconium nitride (c-ZrN) phase, representing (111), (200), (220), (311), and (222) planar orientations, respec- tively. These results are in agreement with the JCPDS PDF #31-1493 reference. Obviously, ZrN (200) peak is dominant indicating that the pre- ferred orientation is ZrN (200). The residual diffraction peaks at 2θ ≅ 44.55o and 64.61o correspond to (110) and (200) planes of Fe-Cr (JCPDS PDF# 34-0396) and the weak peak at 2θ ≅ 42.83o corresponds to (202) plane of Chromium Iron Carbide (Fe,Cr)3C7 phase (JCPDS PDF# 05-0720). These residual phases were contributed by SKD11 steel substrate due to the thinness of ZrN coating film. Clearly, the results of the XRD verified that the coating is composed of ZrN.
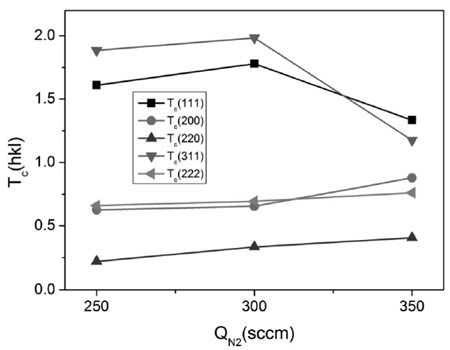
Fig. 3 shows the variation of the texture coeffi- cients of the ZrN film with nitrogen flow rate. When the nitrogen flow rate increases, the texture coefficient Tc(hkl) of (200), (220) and (222) planes of the ZrN thin film increases gradually. The texture coefficients of (111) and (311) planes got the highest value at the nitrogen flow rate of 300 sccm. The changing of the Tc(111) and Tc(311) seems to be correlated with the changing of the hardness and protective efficiency.

Fig. 4 shows the effect of nitrogen flow rate on hardness of ZrN films deposited on SKD11. The ZrN film exhibited a maximum hardness of 2288 HV at the nitrogen flow rate of 300 sccm. Effect of nitrogen flow rate on the properties of ZrN films deposited by arc ion plating process was discussed by Mingsheng Li et al. [11]. The morpholo- gy was explained based on the assumption of “tar- get poisoning”. When nitrogen flow rate increase then N2 partial pressure is high enough, a thin layer of zirconium nitride will be formed on the surface of the target (which called “target poisoning”). The melting point of nitride is much higher than that of the metallic target, resulting in decreasing droplet, hence, the hardness of the film increased. But when N2 partial pressure is too high (350 sccm), the excessive high N2 partial pressure makes the forming of ZrN °Ccur in the space of chamber instead of on the SKD11 surface, which decreases the density of plasma and led to weakened ion bombarding effect and hardness reduction of film deposited at high nitrogen flow rate.

Fig. 5 shows the Tafel plots of the uncoated and coated samples studied in 3 %NaCl solution. As one can see that the coated sample has a higher corrosion potential and lower corrosion current density compared to the uncoated sample.
The corrosion current density (icorr) is an very important parameter. It is normally proportional to the corrosion current density measured via polar- ization. The lower the icorr, the lower corrosion rate of the sample is. In the present test, the icorr values of the coated samples obtained are always less than the bare SKD11 steel (table 2). This result indicates that the ZrN coating deposited by CAPE technique can effectively improve the anticorrosion property of SKD11 steel.
The protective efficiency [12] of the films, Pi (%), can be calculated by eq. (1).
Pi (%) = [1 – icorr / iocorr] 100 (1)
where icorr and iocorr represent the corrosion current density in the presence and absence of the coating, respectively.
Table 2. Corrosion test results of the bare SKD11 sample and the coated ones at the different nitrogen flow rate
Sample | QN2 (sccm) | Ecorr. (mV) | Icorr. (A) | Protective efficiency, Pi (%) |
SKD11 | – | -456,1 | 48,80 | – |
ZrN on SKD11 | 250 | -360,4 | 6,20 | 87.28807 |
300 | -334,2 | 6,06 | 87.59561 | |
350 | -338,6 | 6,81 | 86.05585 |
4. CONCLUSION
ZrN film was successfully deposited on SKD11 substrate by method of cathodic arc plasma evaporation. The coating is composed of ZrN phases, possesses the cubic structure with (200) preferred orientation. Vickers hardness of different samples is in the range 1605÷2288 HV when nitrogen flow rate is in the range of 250÷350 sccm. The potentiodynamic polarization test has been performed to evaluate the effect of N2 flow rate variation on the corrosive resistance of different samples. The ZrN coating deposited by CAPE method can effectively improve the anticorrosion property of SKD11 steel with protective efficiency up to 87%.
ACKNOWLEDGEMENT
This research is funded by the Hanoi University of Science and Technology (HUST), under project T2017-PC-064.
REFERENCES
- Deng Jianxin , Liu Jianhua, Zhao Jinlong, Song Wenlong, Niu Ming; Friction and wear behaviors of the PVD ZrN coated carbide in sliding wear tests and in machining processes, Wear, 264, 2008, 298-307
- R. Hubler, A. Cozza, T. L. Marcondes, R. B. Souza, and F. F. Fiori, Wear and corrosion protection of 316-L femoral implants by deposition of thin films, Surf. Coat. Technol., 142-144, 2001, 1078-1083.
- Deng Jianxin, Liu Jianhua, Zhao Jinlong, Song Wenlong; Wear mechanisms of PVD ZrN coated tools in machin- ing, International Journal of Refractory Metals & Hard Materials, 26, 2008, 164-172.
- H. Jiménez, E. Restrepo, A. Devia; Effect of the substrate temperature in ZrN coatings grown by the pulsed arc technique studied by XRD, Surface & Coatings Technology, 201, 2006, 1594-1601.
- R. J. Rodríguez, J. A. García, A. Medrano, M. Rico, R. Sánchez, R. Martínez, C. Labrugère, M. Lahaye, A. Guette; Tribological behaviour of hard coatings deposited by arc-evaporation PVD, Vacuum, 67, 2002, 559-566.
- H. M. Tung, J. H. Huang, D. G. Tsai, C. F. Ai, and G. P. Yu; Hardness and residual stress in nanocrystalline ZrN films: Effect of bias voltage and heat treatment, Mater. Sci. Eng. A, 500, 2009, 104-108.
- M. Zhang, X. G. Hu, X. X. Yang, F. F. Xu, K. H. Kim, and Z. G. Shao; Influence of substrate bias on microstruc- ture and morphology of ZrN thin films deposited by arc ion plating, Trans. Nonferrous Met. Soc. China (English Ed.), 22, 2012, s115-s119.
- J. H. Huang, C. H. Ho, and G. P. Yu; Effect of nitrogen flow rate on the structure and mechanical properties of ZrN thin films on Si(100) and stainless steel substrates, Mater. Chem. Phys., 102, 2007, 31-38.
- J. Du, P. Zhang, Z. Cai, and J. Zhao, The influence of substrate-target orientation on the properties of ZrN films deposited by arc ion plating, Phys. Procedia, 18, 2011, 181-186.
- K. Ashok, B. Subramanian, P. Kuppusami, and M. Jayachandran; Effect of substrate temperature on structur- al and materials properties of zirconium nitride films on D9 steel substrates, Cryst. Res. Technol., 44, 2009, 511-516.
- Mingsheng Li, Fuhui Wang£¬Effects of nitrogen partial pressure and pulse bias voltage on (Ti,Al)N coatings by arc ion plating, Surface and Coatings Technology, 167, 2003, 197-202.
- J. Menghani, K. B. Pai, and M. K. Totlani; Corrosion and wear behaviour of ZrN thin films, Tribol. – Mater. Surfaces Interfaces, 5, 2011, 122-128.