Trong công trình này, chúng tôi sử dụng phép phân tích nhiệt với tốc độ nung thay đổi từ 10 đến 40 K/phút để nghiên cứu quá trình kết tinh của bột vô định hình Al87Ni8La5 chế tạo bằng phương pháp phun bột.
Crystallization of Al-Ni-La gas atomized powders
NGUYEN HOANG VIET1, DO NAM BINH2, PHAM NGOC DIEU QUYNH1, NGUYEN THI HOANG OANH*1
1School of Materials Science and Engineering, Hanoi University of Science and Technology, Hanoi
2Ministry of Industry and Trade, Hanoi
Email: oanh.nguyenthihoang@hust.edu.vn
Ngày nhận bài: 4/2/2019, Ngày duyệt đăng: 14/3/2019
ABSTRACT
In this work, the crystallization of gas atomized Al87Ni8La5 amorphous powders was studied by thermal analysis with applying different heating rates, varying from 10 to 40 K×min-1. The X-ray diffraction pattern of gas atomized Al87Ni8La5 powders shows mostly amorphous structure. The Al87Ni8La5 amorphous alloy undergoes a two-stage crystallization process during continuous heating by differential scanning calorimetry. The first transformation, in which fcc-Al crystalline precipitates from the amorphous matrix. In the second transformation, the decomposition of the residual amorphous phase into intermetallic phases of Al11La3 and Al3Ni can be observed by X-ray diffraction analysis. The activation energy of two exothermal events calculated by Kissinger method is 146 and 206 kJ/mol, respectively. The thermal stability of the Al87Ni8La5 amorphous powders grows with increasing heating rate.
Keywords: crystallization, amorphous alloy, gas atomized powder, crystallization kinetics.
TÓM TẮT
Trong công trình này, chúng tôi sử dụng phép phân tích nhiệt với tốc độ nung thay đổi từ 10 đến 40 K/phút để nghiên cứu quá trình kết tinh của bột vô định hình Al87Ni8La5 chế tạo bằng phương pháp phun bột. Mẫu nhiễu xạ tia-X của mẫu bột ban đầu cho thấy vật liệu có cấu trúc gần như vô định hình. Từ kết quả phân tích nhiệt lượng kế vi sai cho thấy hợp kim vô định hình Al87Ni8La5 trải qua hai quá trình tinh thể hóa. Ở quá trình chuyển pha đầu tiên, có sự xuất hiện của tinh thể nano fcc-Al từ nền vô định hình. Trong quá trình chuyển pha thứ hai, có sự chuyển pha từ vô định hình dư thành các pha liên kim Al11La3 và Al3Ni được xác định từ kết quả phân tích nhiễu xạ tia X. Năng lượng hoạt của 2 sự kiện tỏa nhiệt được xác định bằng phương pháp Kissinger tương ứng là 146 và 206 kJ/mol. Độ ổn định nhiệt của bột vô định hình Al87Ni8La5 tăng theo tốc độ nung.
Từ khóa: quá trình kết tinh, hợp kim vô định hình, bột phun từ thể lỏng, động học kết tinh.
1. INTRODUCTION
Amorphous and nanostructured Al-based alloys have attracted widespread attention as potential candidates for structural as well as functional appli- cations due to their high strength combined with low density [1]. It is believed that the strength of Al- based amorphous alloys can be further enhanced if fcc-Al nano-particles are homogeneously dispersed within a certain size and fraction range through pri- mary crystallization [2, 3]. Such nanoscale mixed- phase materials can be obtained directly upon rapid quenching or by partial devitrification of melt-spun amorphous ribbons [1]. In contrast, the alloys become brittle if intermetallic compounds are pre- cipitated as the primary phases [4]. Controlling the type of the primary phase is therefore an interesting subject. Moreover, Al-based amorphous alloys exhibit a low thermal stability and their supercooled liquid region DTx is seldom larger than 30 K. Looking for the Al-based amorphous alloys with high thermal stability and large DTx is of signifi- cance for their applications as structural materials, since this makes it possible to fabricate massive products by warm consolidation of the amorphous powders of these alloys [5]. Among the Al-based amorphous alloys, the crystallization behaviors of Al-Ni-La have been found to be strongly dependent on the compositions [6, 7]. For example, as the Ni content in Al85-xNi9-xLa6 (x = 0÷6) amorphous alloys increases, the primary phase changes from fcc-Al plus metastable bcc-(AlNi)11La3-like phase at x = 2÷6 to single unidentified metastable phase at x = 0 [5]. Single fcc-Al is not obtained in the entire Ni content range but is precipitated from Al87Ni8La5 amor- phous alloy.
In the present work, the structure and crystal lization of the gas atomized powder (GAP) Al87Ni8La5 alloy were studied using differential scanning calorimetry (DSC), X-ray diffraction (XRD), and field emission scanning electron microscopy (FE-SEM).
2. EXPERIMENTAL
Powders with nominal composition of Al87Ni8La5 were prepared using the “Nanoval” process at NANOVAL GmbH & Co. KG, Berlin (Germany). The master alloy was prepared from pure elements Al (99.999%), Ni (99.95%) and La (99.5%) by induction melting using a high frequency electromagnetic levitation furnace under a puri- fied argon atmosphere. The levitated melt was kept at high temperatures until the surface oxide skin broke up. After holding of 2 to 7 min, the current was switched off and the levitated melt fell down into a water chilled copper crucible, where it solidi- fied forming a crystalline ingot. This procedure was repeated several times to ensure the homogeneity of the alloy. Then, the melt of the Al87Ni8La5 alloy was heated up to approximately 1350 K, and was subsequently gas-atomized under argon gas. The gas-pressure was controlled manually and could reach a maximum value of 30 bar. Atomization yielded two powder fractions: a coarser major pow- der fraction collected in the atomizer recipient and a finer minor powder fraction collected in the cyclone. A slow oxidation of the as-atomized powder was allowed by flooding the atomizer with air.
The microstructure of GAP was characterized by FE-SEM using a JEOL JSM 6500 F micro- scope. Particle size distribution of the sample was measured using a Malvern Panalyticals’s Mastersizer 2000 laser diffraction analyzer. The crystallization of amorphous powders was studied by DSC in a non-isothermal mode with a NET- ZSCH STA 409C under a continuous flow of puri- fied argon gas. DSC was conducted at heating rates of 10, 20, 30 and 40 K/min to study the crystallization kinetics of the amorphous alloys. The XRD analysis was performed using RIGAKU RINT-2000 diffractometer with Cu-Kα radiation (λ = 0.15405 nm) to study the phase transformations upon subsequent heating.
3. RESULTS AND DISCUSSION
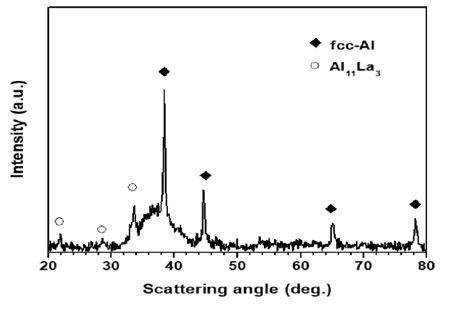
Fig. 1 gives the XRD pattern of GAP Al87Ni8La5 alloy. The XRD pattern shows a broad diffuse halo suggesting the formation of an amorphous phase coexisting with fcc-Al crystal and a minor volume fraction of Al11La3 intermetallic phase.

The SEM images of GAP alloy at different magnifications can be seen in Fig. 2. Powder particles have a spherical shape and smooth surface. Fig. 2b depicts a powder particle with a diameter of about 10 µm with some single satellites with a size of approx- imately 1 to 2 µm on the powder surface. The com- position of GAP alloy measured on single particle by EDS/SEM in Fig. 3 was Al, Ni and La elements.

GAP Al87Ni8La5 alloy
Particle size distribution of GAP Al87Ni8La5 alloy was also analyzed by means of laser light-scattering instrument as shown in Fig. 4. The powder sam- ple has a bimodal distribution including: fine powder particle size in the range of 1.2 ÷ 4.0 mm (P1 distribution) and larger powder particle size in the range of 10 ÷ 50 mm (P2 distribution), as shown in SEM images (Fig. 2). The average particle size d0.5 of the GAP alloy powder is about 16.15 mm.
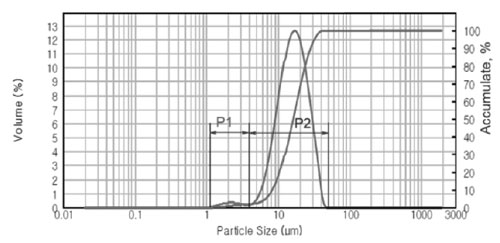
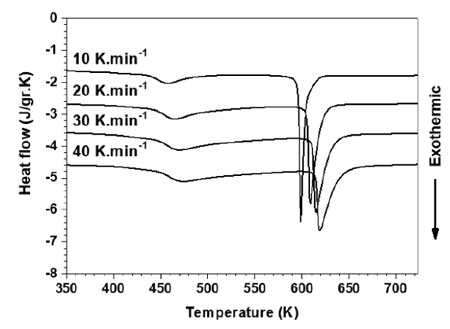
Crystallization of the GAP powders was studied by using a DSC. Fig. 5 illustrates the DSC curves of GAP Al87Ni8La5 alloy at different heating rates. Apparently, two exothermic peaks exhibited distinct two-step crystallization process. The onset crystallization temperature (Tx) determined by the tangent method and the crystallization peak temperature (Tp) at different heating rates are listed in Table 1.
Table 1. The onset (Tx) and peak (Tp) temperatures under continuous heating
Heating rate(K.min-1) | Temperature (K) | |||
Tx1 | Tp1 | Tx2 | Tp2 | |
10 | 439 | 457 | 595 | 599 |
20 | 446 | 465 | 605 | 609 |
30 | 447 | 470 | 611 | 615 |
40 | 449 | 474 | 615 | 619 |
It is noted that the Tx and Tp shift to higher temperature with the increasing heating rate, indicating that the crystallization displays significant dependence on the heating rate during continuous heating. The difference of each crystallization step can be evaluated by the apparent activation energy. The apparent activation energy of the two exothermic peaks is determined by using Kissinger method [8] as follows:
where Ec is the activation energy of crystallization, Tp is the temperature of the exothermal peak, α is the heating rate, and R is the gas constant.
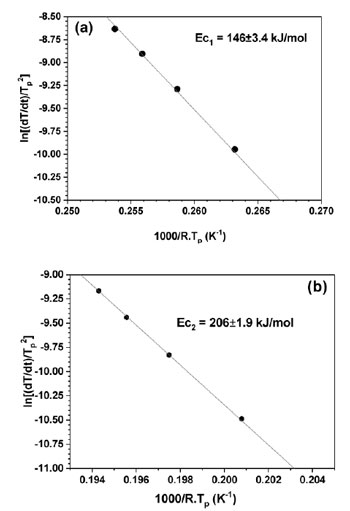
Fig. 6 presents the Kissinger plots by using linear function of ln(α/Tp2) versus (1000/Tp) yielding activation energy Ec of the first and second exothermic heat releases as 146±3.4 and 206±1.9 kJ.mol-1, respectively. The value of Ec for the first exothermal event is almost similar to the value for the self-diffusion energy of aluminum [9]. The activation energy of the second crystallization peaks is higher than that of the first exothermal event due to the decomposition of residual amorphous phase into intermetallic phases as F. Ye [10] reported for Al89La6Ni5 alloy. To understand the meaning of the two exothermic peaks of Al87Ni8La5 alloy during crystallization, the structural evolution of the heat treated Al87Ni8La5 amorphous powder was investigated by XRD. The amorphous Al87Ni8La5 alloy powder was annealed at 533 and 700 K with heat- ing rate of 40 K/min. The XRD results of annealed powder were shown in Fig. 7. Crystalline phase of fcc-Al was identified by XRD for sample after annealing at 533 K (Fig. 7b) which is similar to XRD pattern of as-received powder (Fig. 7a). At higher annealing temperature of 700 K crystalline fcc-Al and intermetallic phases can be detected (Fig. 7c). Two-step crystallization behavior was observed under continuous heating of Al87Ni8La5 GAP alloys: amorphous Al87Ni8La5 phase + minor of fcc-Al and Al11La3 phases → fcc-Al + amorphous matrix + minor Al11La3 phase → fcc-Al + intermetallic phases of Al11La3 and Al3Ni.

4. CONCLUSION
GAP Al87Ni8La5 alloy has bimodal particle size distribution and average particle size of about 16.15 mm. Thermal analysis revealed the GAP alloy crystallizes through two stages, or two exothermic reaction peaks upon continuous heating. The onset and peak crystallization temperatures of alloy shift to higher temperature with the increasing heating rate, indicating that the crystallization displays significant dependence on the heating rate. The first stage exothermic reaction is the precipitation of fcc-Al from amorphous matrix with activation energy of 146 kJ/mol. The second exothermic event corresponds to the decomposi- tion of the remaining amorphous phase to inter- metallic phases of Al11La3 and Al3Ni with higher activation energy of 206 kJ/mol.
ACKNOWLEDGEMENT
This research is funded by Vietnam National Foundation for Science and Technology Development (NAFOSTED) under grant number 103.02-2017.366.
REFERENCES
- A. Inoue; Amorphous, nanoquasicrystalline and nanocrystalline alloys in Al-based systems, Progress in Materials Science, 43(5), 1998, 365-520
- Y. He, S. J. Poon, G. J. Shiflet; Synthesis and properties of metallic glasses that contain aluminum, Science, 241(4873), 1988, 1640
- A. Inoue, K. Ohtera, A. -P. Tsai, T. Masumoto; Aluminum-based amorphous alloys with tensile strength above 980 MPa (100 kg/mm2), Japanese Journal of Applied Physics, 27(Part 2, No. 4), 1988, L479-L482
- Z. C. Zhong, X. Y. Jiang, A. L. Greer; Micro structure and hardening of Al-based nanophase composites, Materials Science and Engineering: A, 226-228,1997, 531-535
- Z. H. Huang, J. F. Li, Q. L. Rao, Y. H. Zhou; Effects of replacing Ni by Co on the crystallization behaviors of Al–Ni–La amorphous alloys, Intermetallics, 16(5), 2008, 727-731
- T. Benameur, A. Inoue; Amorphization of aluminum base multicomponent systems by ball milling (overview), Materials Transactions, JIM, 36(2), 1995, 240-250
- K.L. Sahoo, M. Wollgarten, J. Haug, J. Banhart; Effect of La on the crystallization behaviour of amorphous Al94−xNi6Lax (x=4–7) alloys, Acta Materialia, 53(14), 2005, 3861-3870
- L. Heireche, M. Belhadji; The methods Matusita, Kissinger and Ozawa in the study of the crystallization of glass- es. The case of Ge-Sb-Te alloys., Chalcogenide Letters, 4(2), 2007, 23-33
- X. Wang, D. Wang, B. Zhu, Y. Li, F. Han; Crystallization kinetics and thermal stability of mechanically alloyed Al76Ni8Ti8Zr4Y4 glassy powder, Journal of Non-Crystalline Solids, 385, 2014, 111-116
- F. Ye, K. Lu; Crystallization kinetics of Al–La–Ni amorphous alloy, Journal of Non-Crystalline Solids, 262(1), 2000, 228-235.